Hope’s Manufacturing Process
Materials
Hope’s secure exterior windows are fabricated from 10- or 12-gauge A60 painted sheet steel, 12- or 14-gauge 302/304 grade stainless steel, and solid, hot-rolled steel.
Fixed or operable configurations are available in traditional steel, thermally-improved or thermally-broken construction.
Finishing
The strength, versatility, and performance of Hope’s steel windows and doors are enhanced and protected by the industry’s most comprehensive multi-stage finishing process.
Our industry leading pretreatment and finishing process can be field applied and complies with ASTM coatings performance criteria including abrasion, adhesion, exterior exposure, graffiti resistance, humidity, QUV, and salt spray.
Technology
Hope’s continually invests in technology, equipment and methods to enhance quality and product performance.
Custom Fabrcation
All products are custom designed and fabricate to met the unique needs of each customer.
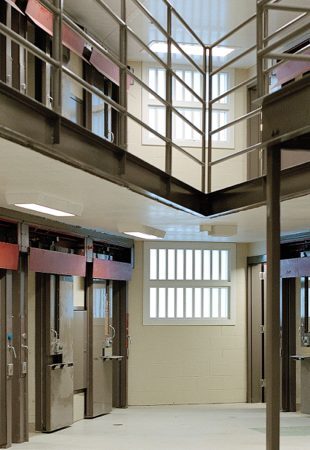
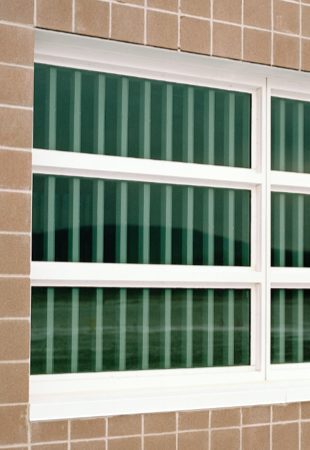
Choose Hope’s for strong, durable, and rigorously tested steel security windows.
The Hope’s Manufacturing Process
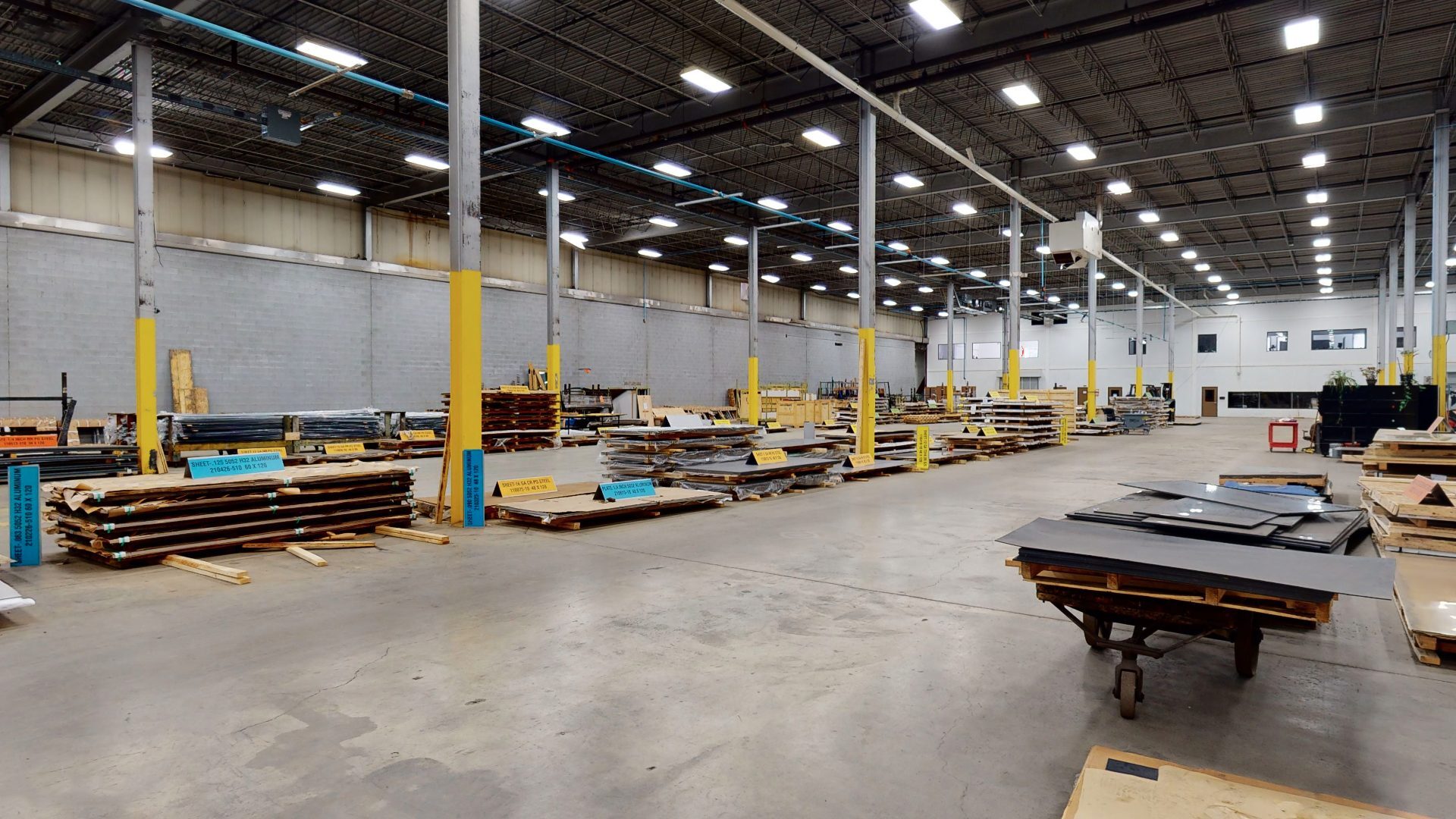
Raw material — hot-rolled steel profiles, sheet steel, tool resistant steel rods, flats and tubes use to fabricate and configure Hope's security windows.
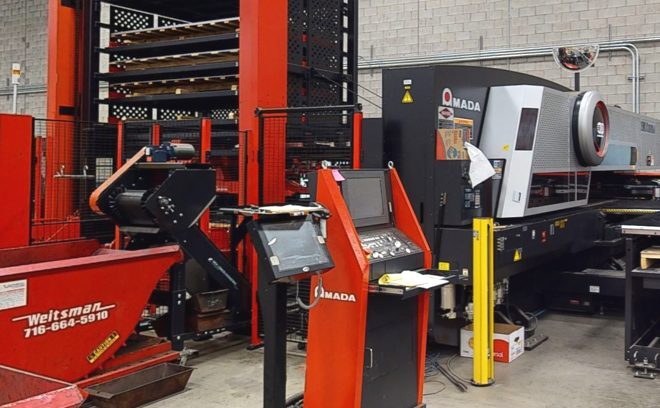
33-Ton Turret Punch & Hybrid Laser Combination
The Amada EMLK 3610NT CNC Laser Combo Punch is equipped 58 tool stations and a 4,000 watt laser. It also has a automated loading/unloading system for unmanned loading of raw sheet steel and the collection, sorting, and stacking of laser cut parts.
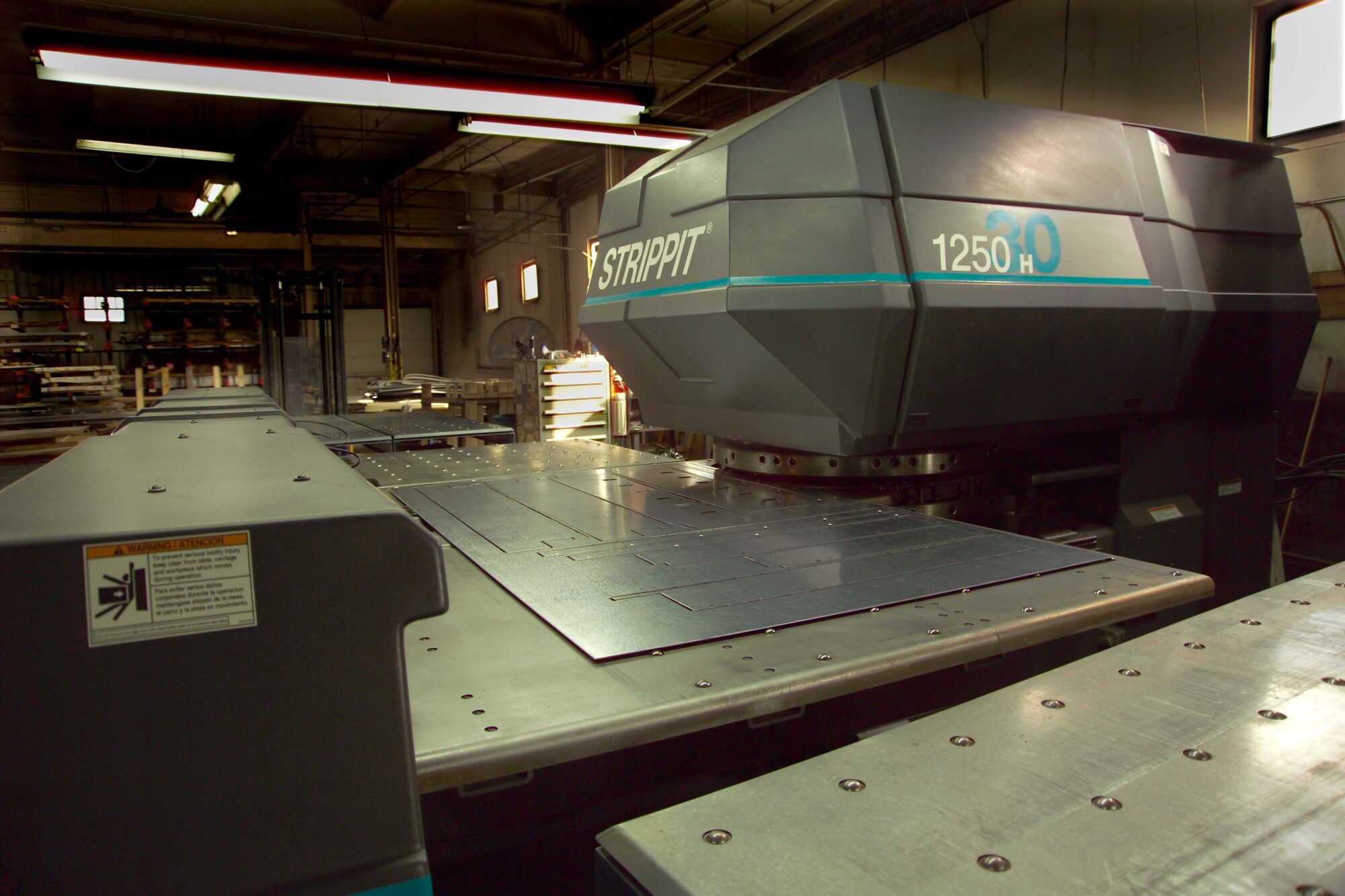
33-Ton Turret Punch Press
The Strippit 1250 H/30 CNC Punch Press holds 42 different tools and has two auto-index stations that allow tools to be turned automatically to the required degree. Steel sheets are manually loaded. After the operator ensures all tooling is correct, the machine runs the punching program with automatic tool changes.
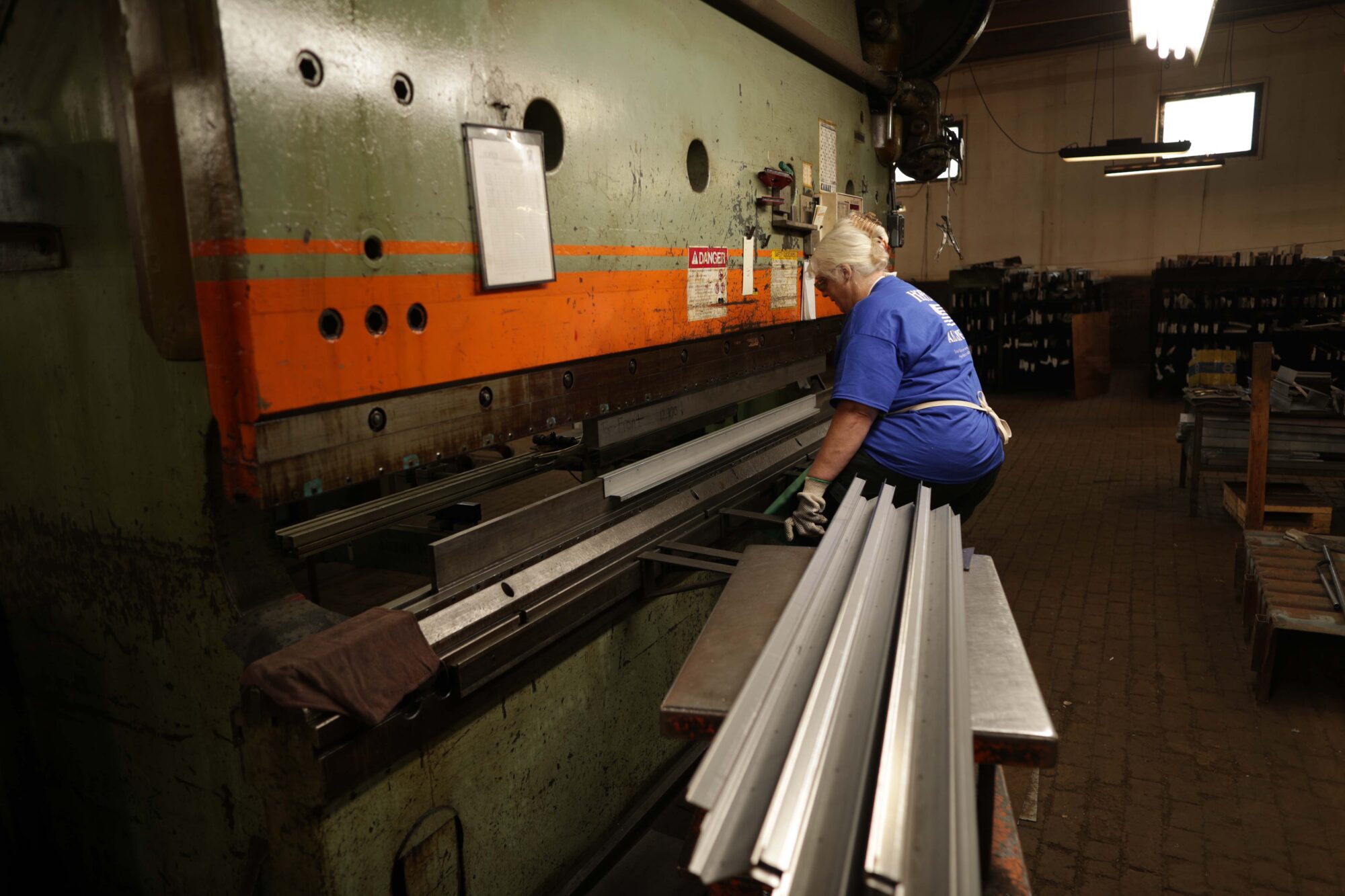
Once the sheet steel has been cut, parts are sent to press brake for bending into the proper shape to form the frames and vents.
1 Sheet Metal Storage
We maintain a supply of all steel raw material used to fabricate and configure Hope' security windows to accommodate the tight shipping needs of our customers.
2 Sheet Metal Layout and Machining
Layout for Hope’s specialty products is done by our Engineering Department using CAD, then sent to Manufacturing. The computer design is unfolded, to be cut on various custom machines, punch presses are used along with along with numerous lasers and machining centers to create the final unfolded parts.
3Sheet Metal Forming
Once the sheet steel has been cut, parts are sent to the press brake for bending into the proper shape to form the frames and vents.
4 Tool Resistant Steel Cutting
Tool resistant steel rods and flats require special equipment. The initial cutting is done using detail cutting sheets. The cutting sheets contain information such as contract number, profile type, bar length, number of bars, type of cut to be made and window or vent type.
5 Welding
Welders use blueprints and cutting sheets to build each project. Tight tolerances are held, and the project starts to take shape. All seams are continuously back welded for maximum strength and weather tightness.

Tool resistant steel rods and flats require a special saw to cut, as a normal blade cannot penetrate this steel.
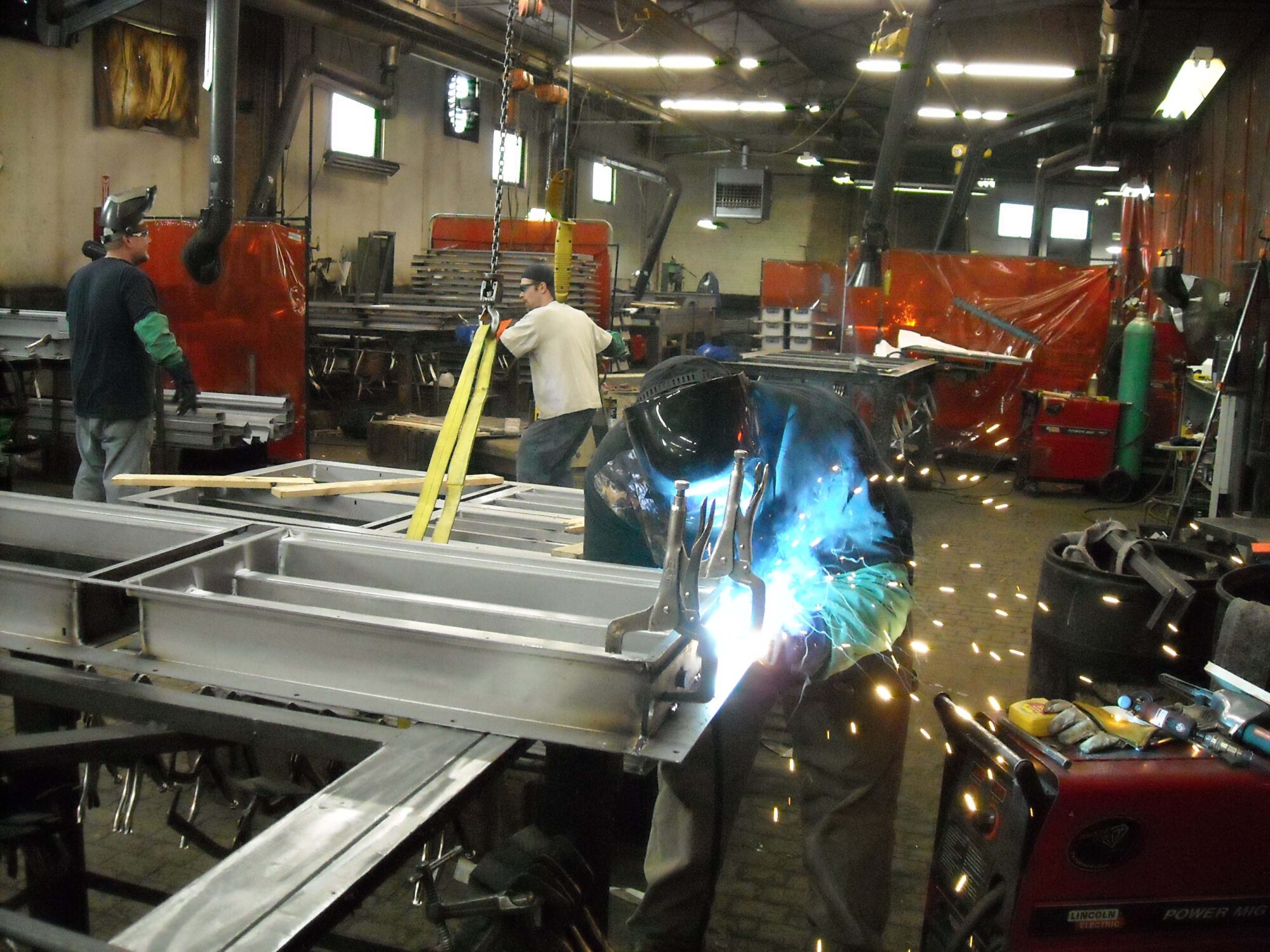
Welders use blueprints and cutting sheets to build each project. Tight tolerances are held, and the project starts to take shape. All seams are continuously back welded.
Fully Welded Construction
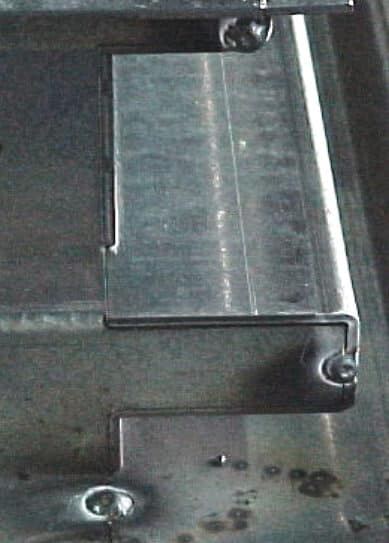
Tack Welded Construction
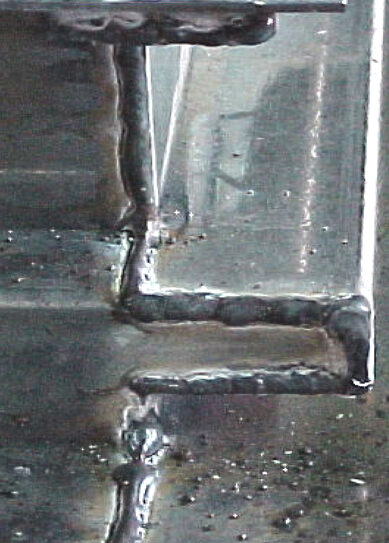
Fully Welded Construction
A major point of differentiation for Hope’s products is superior strength. This strength is achieved by employing full-depth welding to permanently join metal framing members. Hope’s standard welding process for sheet steel components utilizes a continuous weld to bond and seal corners ensuring maximum strength and weather tightness for the life of the product. This process is recommended for exterior windows and or those frames requiring ASTM compliance with air, water and impact.
For hot-rolled steel, Hope’s utilizes a fusion welding process to merge corner pieces into a single piece of steel using hydraulic pressure and electricity. The fusion welded corner is unique to Hope’s and offers unmatched strength. The fusion welded corner withstands twisting of a full 360° without failure.
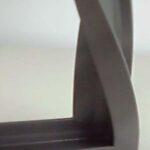
Fusion Welded Corner
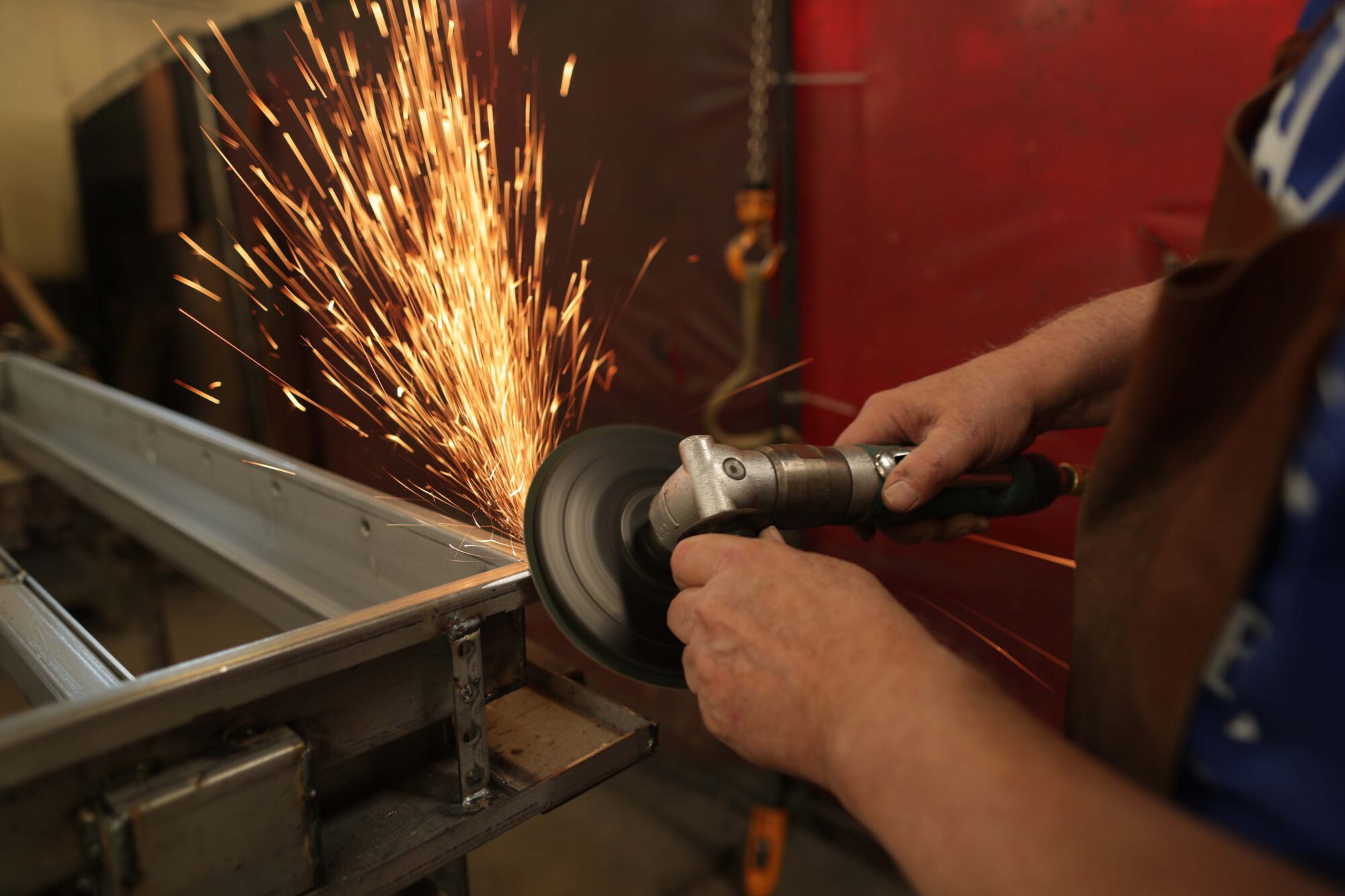
In this department, the finishing touches are applied. A variety of tools are used to ensure a level, clean, and aesthetically-pleasing surface.
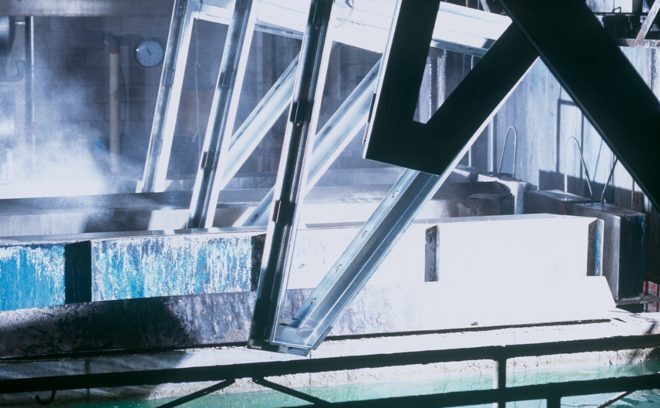
Petierunt uti sibi concilium totius galliae in diem certam indicere quo usque tandem abutere, catilina, patientia nostra unam. Incolunt belgae aliam aquitani tertiam praeterea iter est quasdam res quas ex communi.
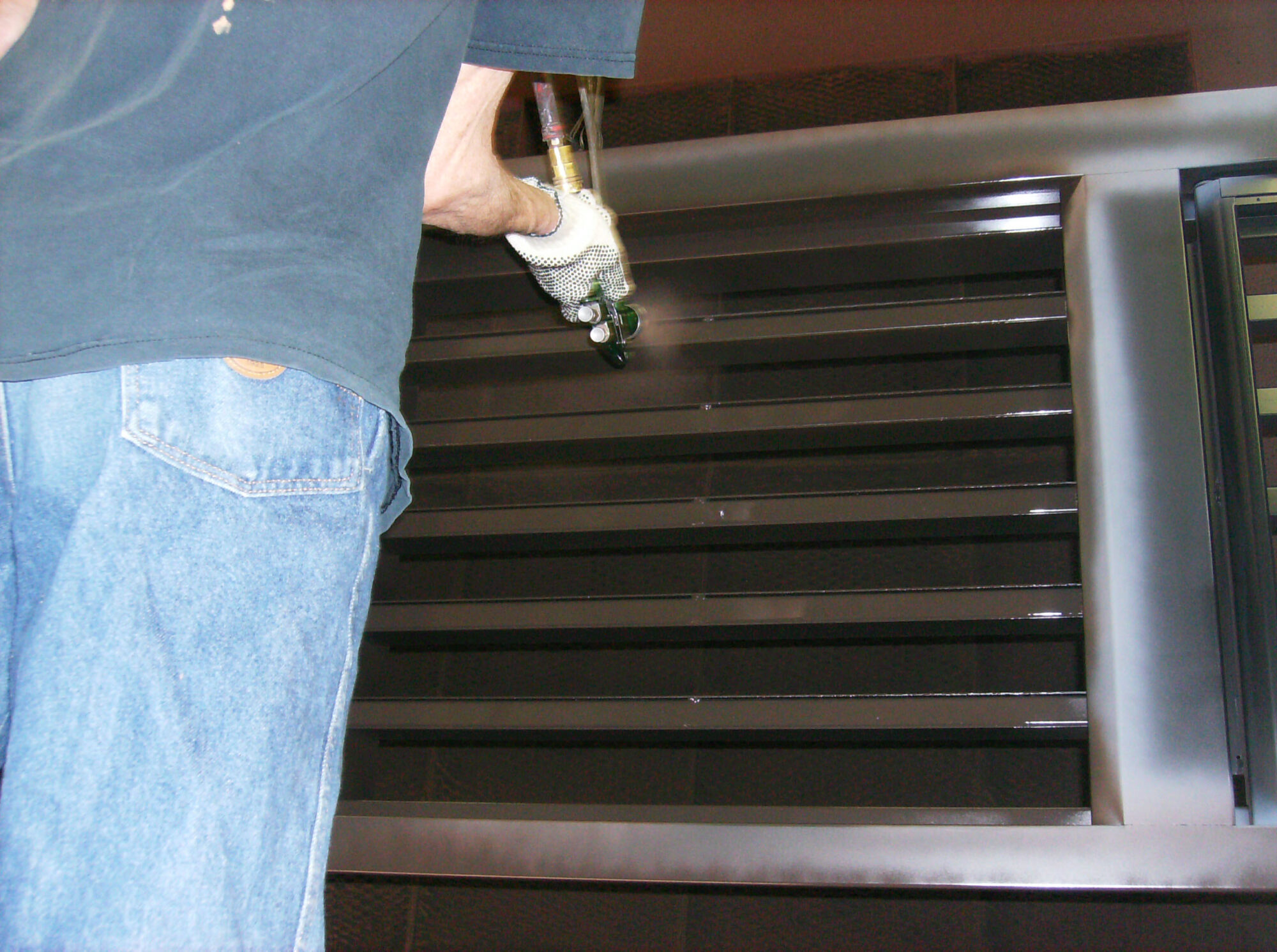
The first two sprayers apply the first coat of paint (about 40%) of the total coat. Six minutes later, the next two sprayers apply the final coat of paint bonding all edges and corners before completing the face. As the material moves toward the baking oven, the solvent is given time to escape from the wet paint resulting in a smoother and more uniform appearance.
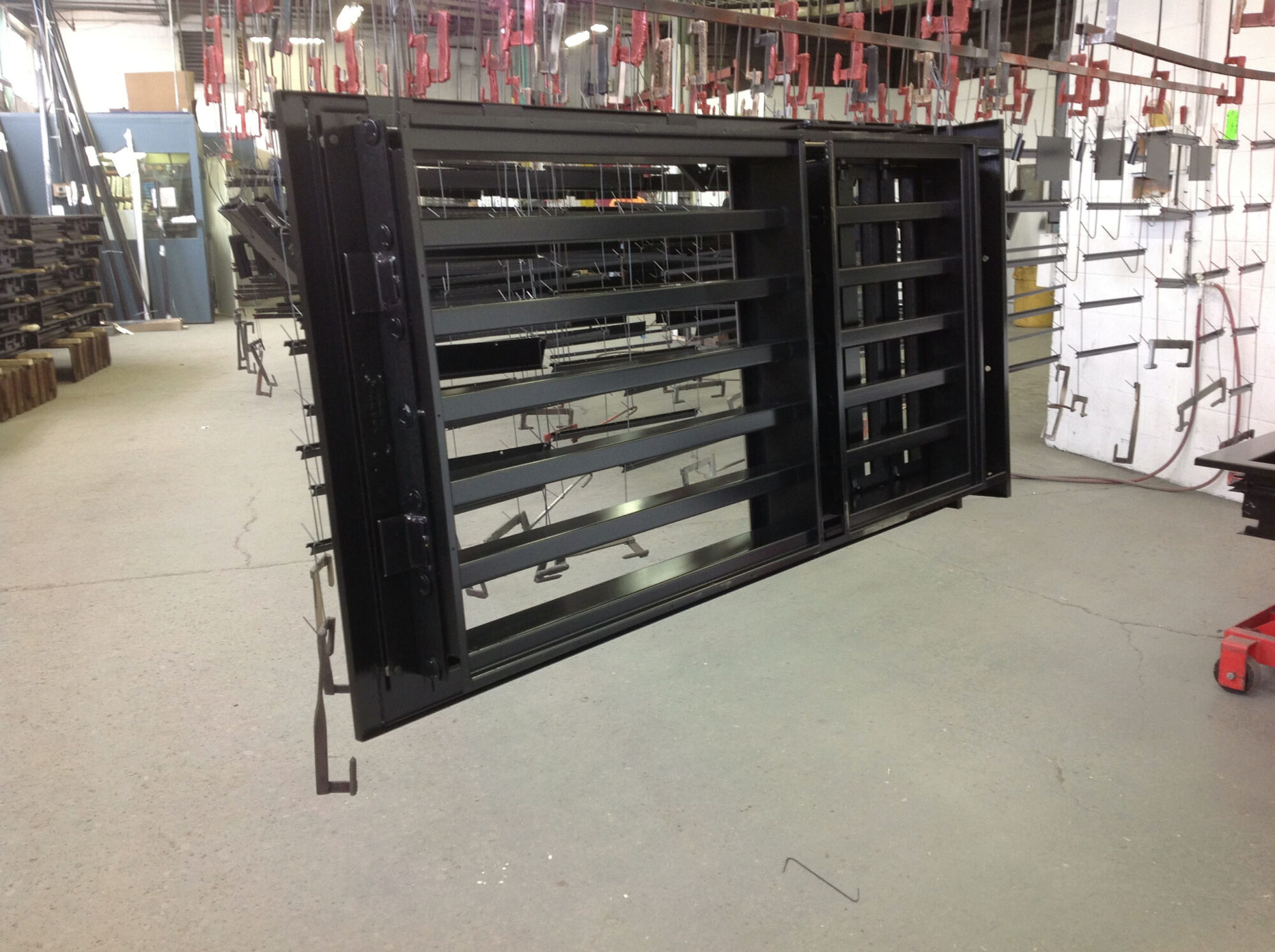
Although the Satin VOC paint can be air cured, to accelerate the drying process, we bake the material in a 240° F oven for 20 minutes. After a cooling down period, the material is inspected for finish defects and padded for protection.
6 Clean and Grind
7 Electrocoat Pretreatment-
The benchmark of quality protective coatings, emersion electrocoat (electrostatic emersion coating) offers several advantages. It provides a complete, uniform coating – even in corners, on edges, and in hard to reach, partially enclosed spaces of every shape and size – resulting in a superior corrosion resistant cleaning and epoxy priming process.
8Paint Finishing
We use Matthews/PPG Low VOC Satin Acrylic Polyurethane. This product is environmentally responsible as it exceeds the toughest compliance regulations.
E-coated material is hung and inspected before the line moves into the four manual spray booths. The first two sprayers apply the first coat of paint (about 40%) of the total coat. Six minutes later, the next two sprayers apply the final coat of paint bonding all edges and corners before completing the face.
9Paint Oven
Although the Satin VOC paint can be air cured, to accelerate the drying process, we bake the material in a 240° F oven for 20 minutes. After a cooling down period, the material is inspected for finish defects and padded for protection. Throughout our day, we may change colors as many as 15 times drawing from the more than 60,000 colors currently formulated.
10 Final Assembly
Assemblers fit all hardware, trim, glazing bead molding, weatherstripping, and various other components.
11 Packaging and Shipping
Upon completion, all units are carefully wrapped and prepared for shipment. We ship on custom pallets via dedicated carrier to projects throughout the world.
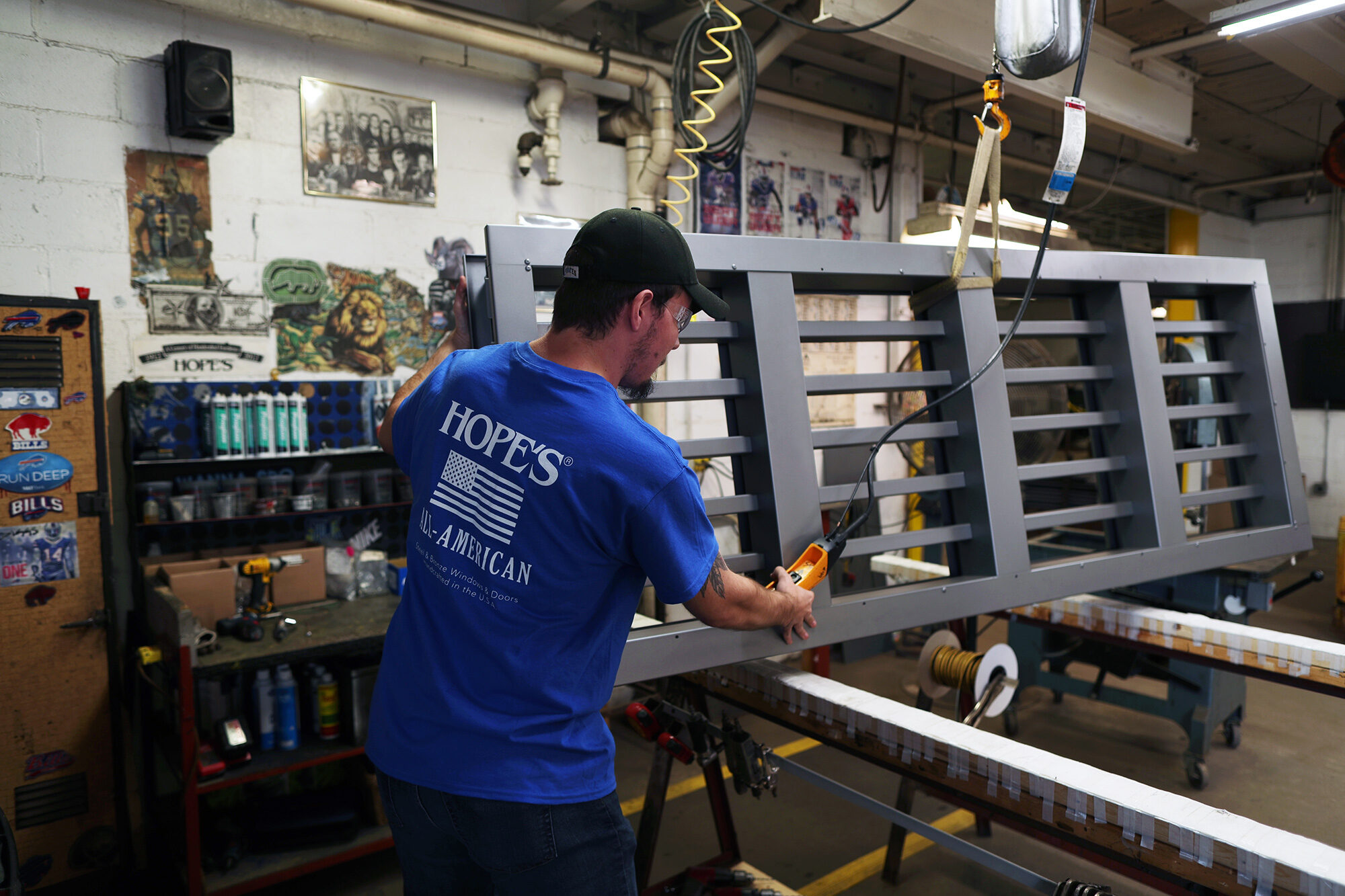
Assemblers fit all hardware, trim, glazing bead molding, and various other secure window components.
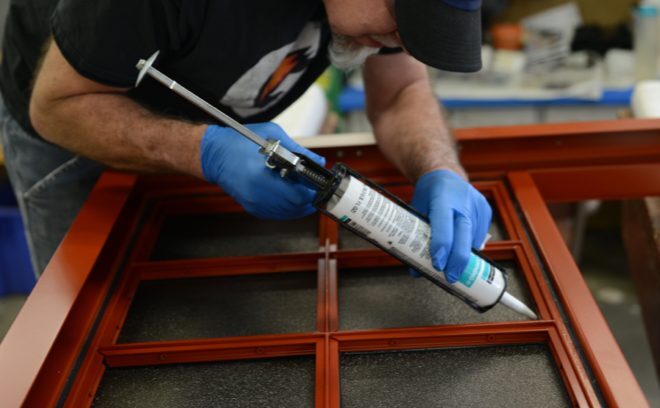
Petierunt uti sibi concilium totius galliae in diem certam indicere quo usque tandem abutere, catilina, patientia nostra unam. Incolunt belgae aliam aquitani tertiam praeterea iter est quasdam res quas ex communi.
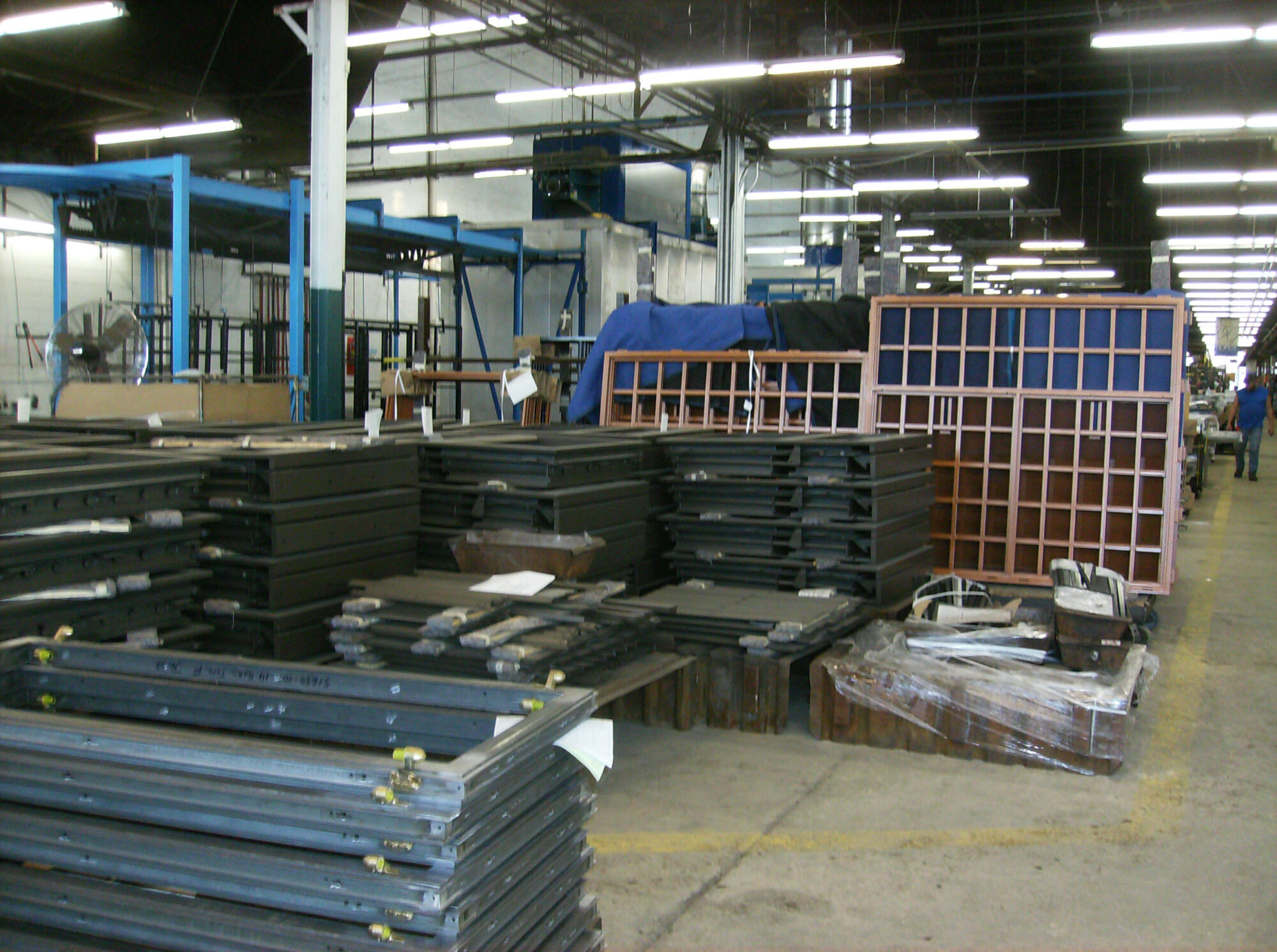
Upon completion, all units are carefully wrapped and prepared for shipment. We ship on custom wooden pallets via common carrier.